液氮低溫箱是將被處理工件置于特定的、可控的低溫環境中,使材料的微觀組織結構產生變化,從而達到提高或改善材料性能的一種新技術的衍生產品。
高速鋼一直是以制造金屬切削刀具而著稱的。自從20世紀60年代開始,日本以汽車工業為中心,試用高速鋼做模具并取得成功,高速鋼的應用范圍不斷擴大。主要采用高速鋼制造冷擠壓模具,其中鉬系高速鋼比鎢系高速鋼韌性更加*。主要工藝難點在于熱處理技術的掌握。
我國使用廣泛的高速鋼是鎢系的W18Gr4V鋼和鎢鉬系的W6Mo5Cr4V2鋼。其傳統淬火回火工藝特點是:高溫淬火后需要一次硬化范圍內回火3次,其缺點是硬度不足。為了改善模具強韌性,近年來高速鋼的傳統淬火回火工藝也發生了變革。
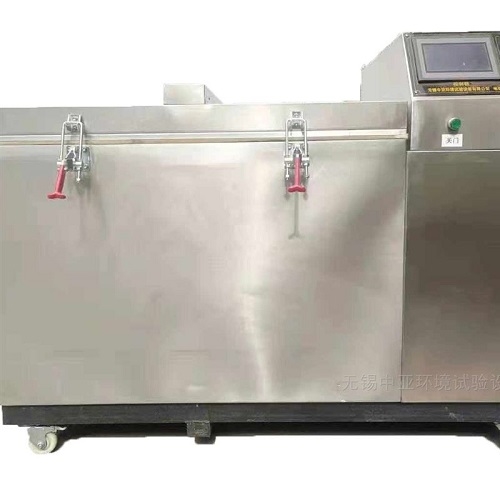
過去工業上采用高速鋼冷處理的目的是將淬火鋼件冷卻到-60℃左右,使鋼內的殘余奧氏體轉變為馬氏體。縮短熱處理生產周期。采用淬火+冷處理+一次回火,經深冷處理后零件的硬度和耐磨性進一步改善。
20世紀70年代以來,對深冷處理的研究更加深人并取得重要成果,有效地利用液氮低溫箱的深冷處理來提高模具的使用壽命、耐磨性及穩定的尺寸。
深冷處理后的組織轉變:
深冷處理后的高速鋼同時引起奧氏體和馬氏體的轉變。其中馬氏體轉心點M1非常低,例如W18Cr4V的M1點為-100℃。因此淬火冷卻到室溫殘留大量的奧氏體,而大量奧氏體的存在會降低鋼的硬度,耐磨性以及熱性能和磁性下降。
實驗證明,回火后,經過液氮低溫箱的深冷處理可以使殘留的奧氏體降低20%左右。表2所示為不同處理工藝對W18Cr4V鋼殘留奧氏體的影響。
通過對-196℃液氮中15min的深冷處理,有關實驗表明,當溫度在-70℃~-75℃到-130℃~-140℃范圍內進行深冷處理時,馬氏體轉變;當冷卻到-196℃時轉變停滯;在-90~-120℃溫度范圍內,出現試樣容積的見效,這就說明了馬氏體已部分分解并在位錯面上析出了碳原子并形成了超顯微碳化物,其基體組織明顯細化。